HAYES & STOLZ LIQUID COATERS
Standard Features:
- Capacities from 3 to 120 Tons Per Hour.
- Full spray pattern without nozzle plugging is insured with air assist liquid spray and large orifice nozzles.
- Can be designed for single or multiple liquids.
- Custom designs for proportioning dry additives are available.
- All components mounted at the factory, pre-plumbed and pre-wired.
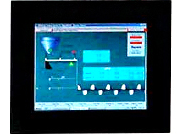
CONTROLS
Dry and liquid flow rate sensing, combined with rapid response ratio control, provides an unusually high degree of accuracy. In addition to process monitoring and control, the unit provides an on screen read out of process events, and stores process data.
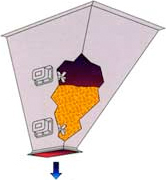
SURGE BIN
A product surge bin with high and low level indicators is used in conjunction with the control system so unit will run only when dry product is available.
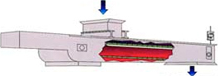
WEIGH FEEDER
Product is conveyed by a drag bar to ensure even, non-surging flow into the spray chamber or directly into the blender. The rate of flow is easily changed by raising or lowering a bed leveling plate or adjusting feeder with the VFD. Self cleaning feeder is wide enough so that only a thin bed of material will feed into the spray chamber. For gravimetric arrangements, the feeder inlet is positioned above the fulcrum point and product flow is measured by a load cell for optimum accuracy.
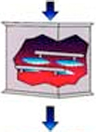
STAINLESS STEEL SPRAY CHAMBER
The dry flow is baffled into a thin stream which free falls through the spray chamber. The product stream is sprayed from both sides to assure maximum coating. The use of air assist spraying ensures penetration, even if the liquid is too low to generate an adequate spray pattern, and allows the use of spray nozzles with large orifices to minimize plugging caused by foreign material.
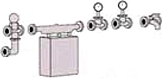
LIQUID ADDITION
Liquid is delivered via a pump with a VFD drive and a flow meter. For gravimetric arrangements a mass flow meter is used with the meter and VFD drive controlled by the system’s main controls providing maximum accuracy and rapid response time.
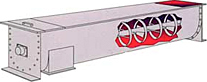
BLENDER
A continuous blender is positioned under the spray chamber to facilitate additional particle-to-particle coating. The blender can be low, medium, or high intensity depending on process requirements.